Objective
Rehabilitate ship berthing cell while maintaining cargo on-load and off-load capabilities.
Highlights
Accomplished rehabilitation while keeping facility operational for entire four-month project
Designed and installed over 100 unique components for the job
Completed project accident and incident free, through over 500 crane lifts, 247 commercial dives, and more than 4,000 square feet of 20,000 psi surface preparation
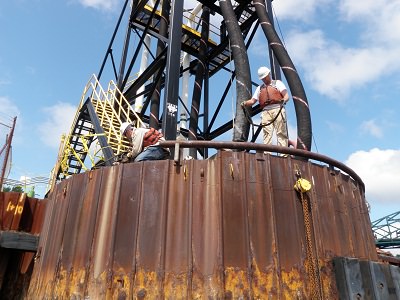
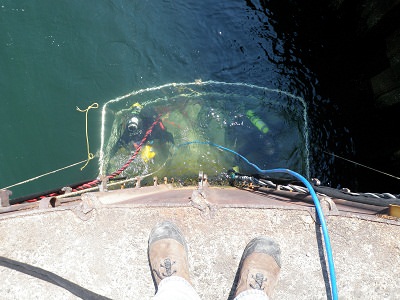
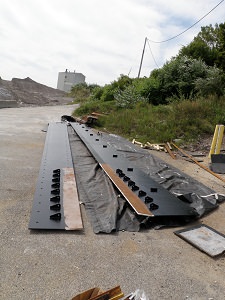
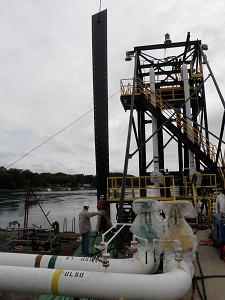
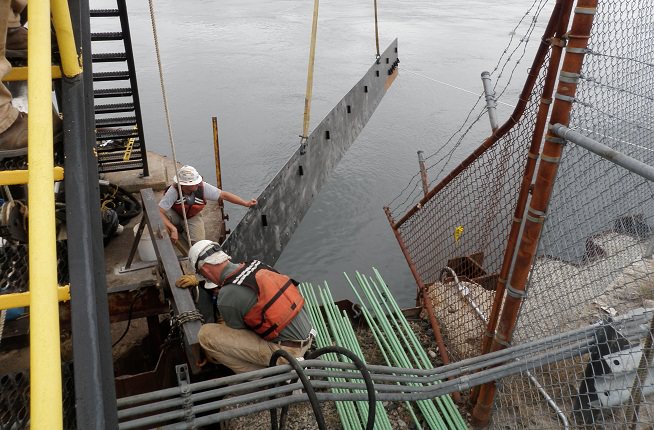
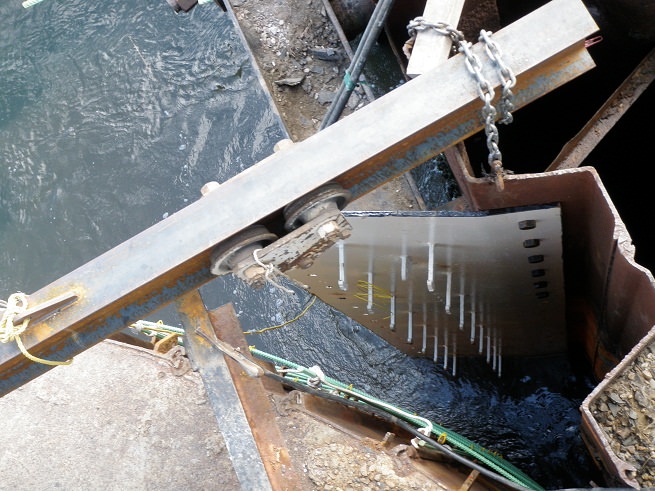
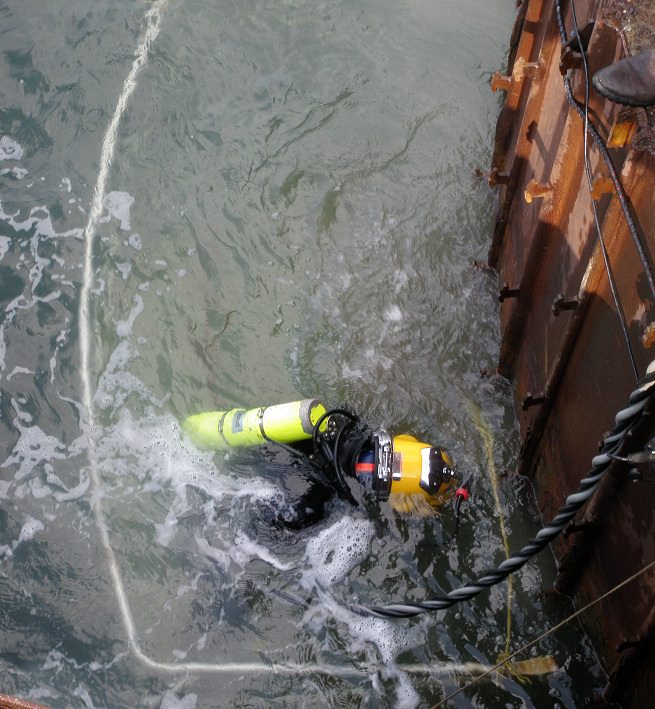
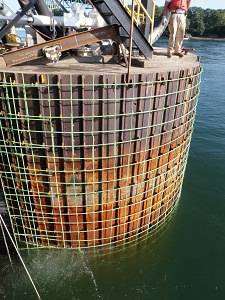
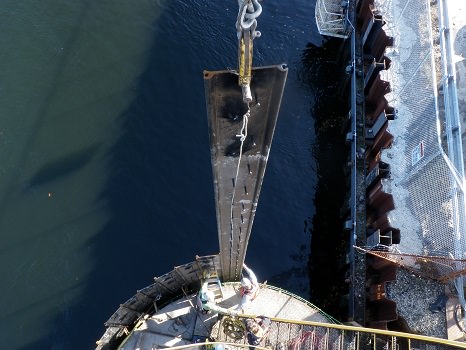
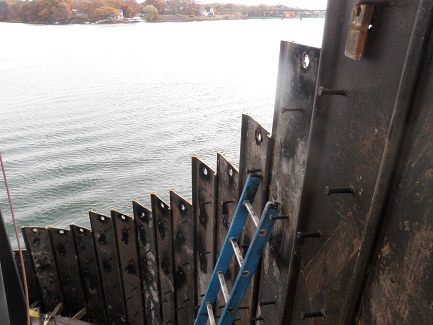
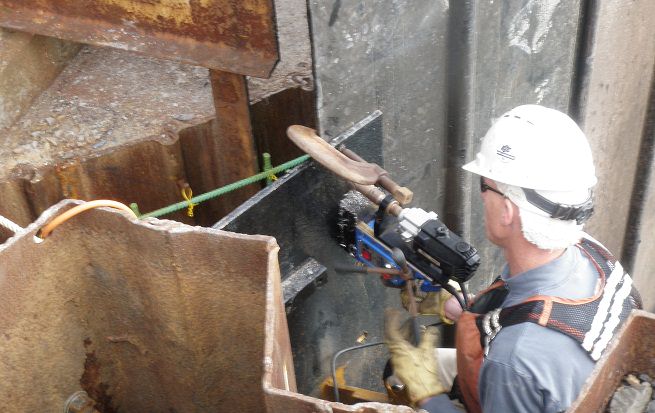
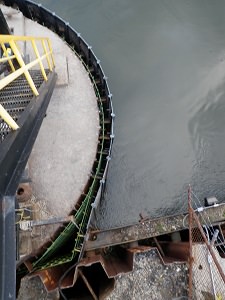
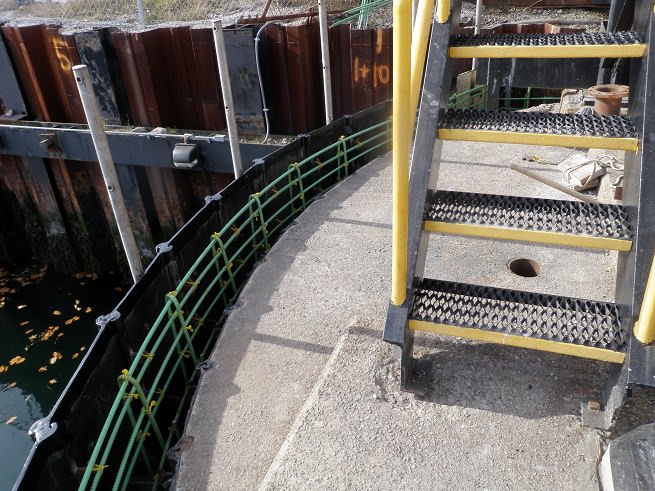
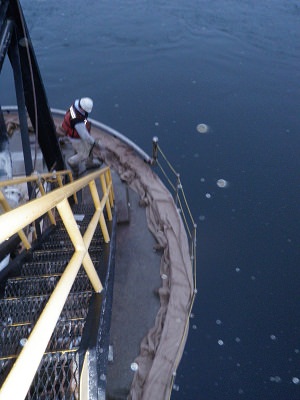
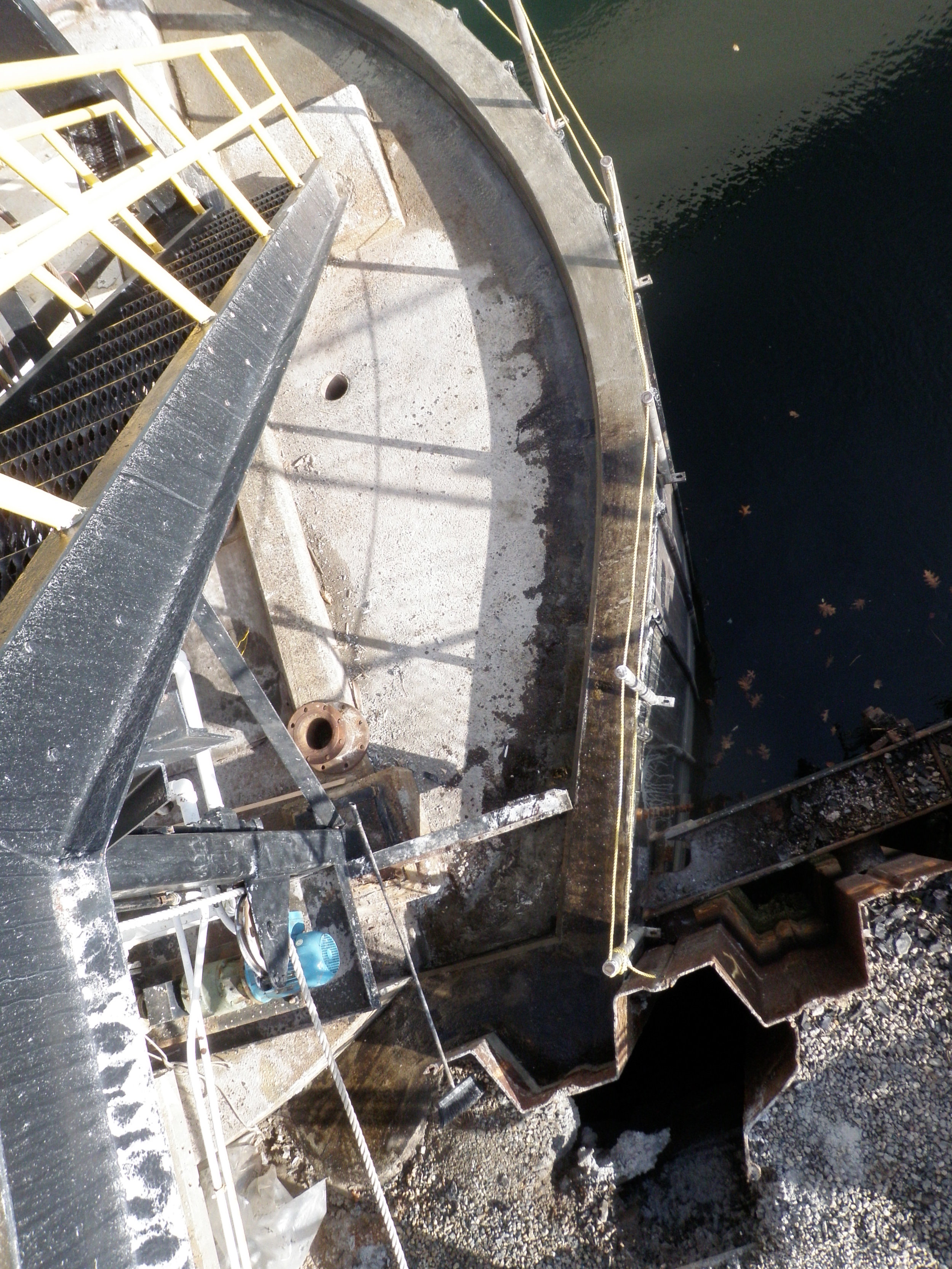
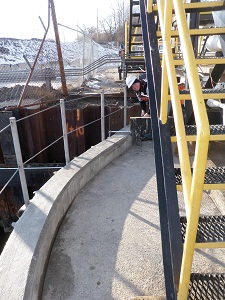
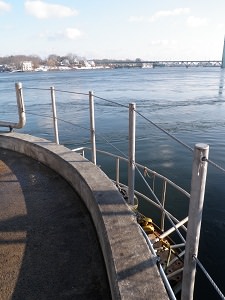
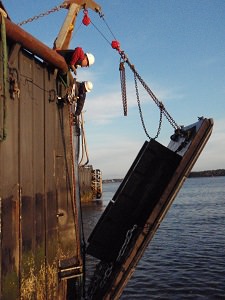
Project Details
Substructure designed and rehabilitated a cellular cargo dam supporting the hose tower used for transferring petroleum cargo from oceangoing vessels on a high-traffic, high-current river. A primary goal of the job was to keep the facility fully operational throughout the four-month construction phase. Substructure accomplished this through close coordination with the facility managers.
Substructure was chosen for this job for our unique combination of engineering, commercial diving, fabrication, and marine construction skills. Employing Substructure as the single contractor for this project eliminated the need for expensive diving subcontractors and gained Substructure’s high-level in-house engineering services, resulting in significant cost savings.
During the design phase, Substructure was faced with the task of tying the new structure directly into the existing, and heavily corroded, sheet pile bulkhead without completely encircling the cell. In response, Substructure engineers completed rigorous stress testing and analysis to mitigate the forces encountered during steel and concrete placement. Testing also took into consideration ways to maximize the life of the structure. The final design included bolting on a transition sheet to interlock the standard sheet pile with the existing structure. Welding was not practical given the age and corrosion level of the existing walls.
In the construction phase, Substructure worked with a small crew (fewer than ten individuals), including engineers, certified commercial divers, welders, and site supervisors. The job required welding a series of rebar tie plates to attach a steel reinforcing structure to the outside of the existing cellular cargo dam. Nelson studs were welded to the new sheet piles before the sheet piles were driven to ensure they would be soundly embedded into the concrete. The gap between the two structures was tremie poured with 250 yards of marine-grade concrete.
The overall job included attaching nearly 3,000 studs, custom designed and fabricated by Substructure, to the surface of the existing cell. Roughly two-thirds of these were attached under water by underwater dive welders. In addition, Substructure designed, built, and installed over 100 different custom components to both overcome various facility obstacles and to ensure an end product that perfectly suited the client.